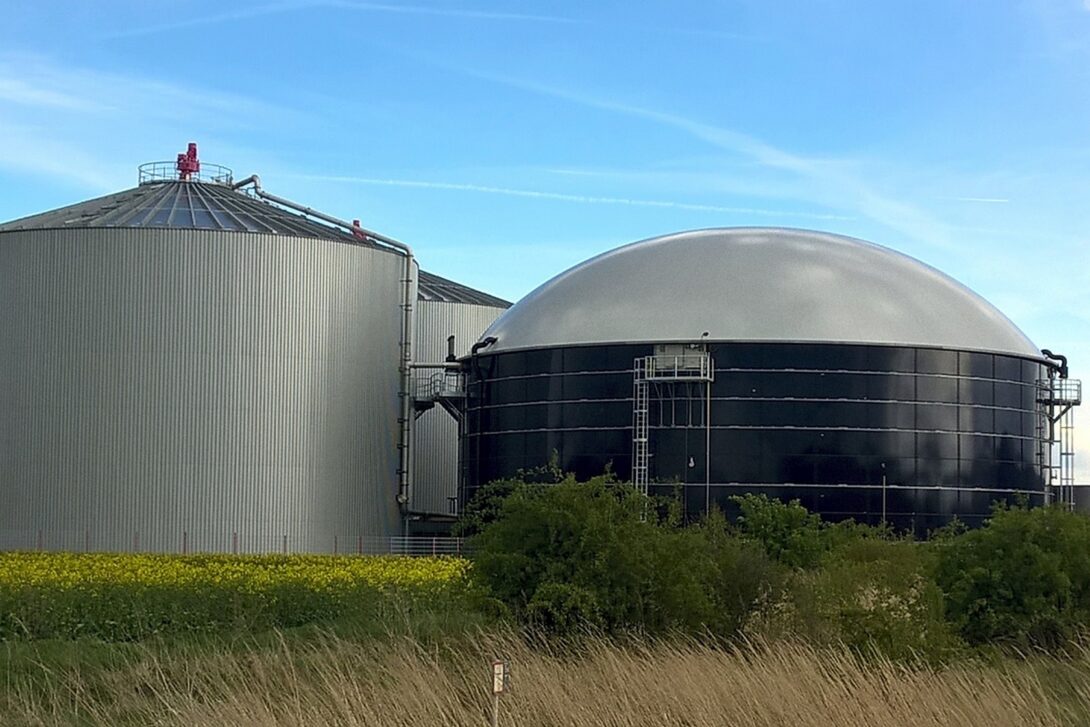
German Flex farm adapts biogas plant to farmers’ needs
Farmer Andreas Rolfs operates a biogas plant on about 235 hectares. Using corn, manure and slurry, the operator generated about 5.4 million kilowatt hours of electrical energy and 4.1 million kilowatt hours of thermal energy before expanding the plant.
In Verbleck, Lower Saxony, ETW Energietechnik increased the capacity of an agricultural biogas plant by building a storage power plant in 2019. The CHP experts were supported by the planning company Energethik from Osnabrück. In addition to the new TCG 2020 V20 flex CHP with biogas engine from MWM with 2 megawatts electric and 2.3 megawatts thermal, ETW installed a combined gas storage for 8,490 and a heat storage for 1,000 cubic meters. The total investment amounted to 1.6 million euros.
Since 2001, farmer Andreas Rolfs has operated a biogas plant on an area of about 235 hectares. Using corn, manure and slurry as feedstock, the operator generated about 5.4 million kilowatt hours of electrical energy and 4.1 million kilowatt hours of thermal energy before the expansion. Since the expansion into a storage power plant, the facility now produces 5.7 million kilowatt-hours of electricity and nearly 5.8 million kilowatt-hours of heat per year. The electricity is fed into the grid, and the waste heat is fed into the district heating network to heat private and municipal buildings and to dry wood chips. Some of the heat is diverted to keep the engine warm when it is not running. This allows the direct marketer to quickly restart the engine when needed and have immediate access to the full power of the CHP unit.
In addition to increasing the production volume, the plant can now also be used flexibly. In return, Rohlfs will receive an additional flexibility premium of 40 euros per kilowatt for the next five years. After that, the farmer can apply for another ten years of EEG through a tendering process if he wishes. His main advantage: Thanks to the CHP Flex, his plant now operates in such a way that electricity and heat can always be provided at the most productive time of day. For this purpose, the biogas plant is controlled by a direct marketer so that the storage tanks are always optimally filled when prices are highest and as much electricity and heat as possible is available.
The plant is operated with desulfurized biogas. For this purpose, the sulfur content is reduced from about 5000 parts per million (ppm) to about 2 ppm. A safety alarm with integrated accumulator stop protects the cogeneration plant if the sulfur content exceeds 2 ppm. This is particularly necessary because the sulfur content can rise more rapidly during flexible operation. After a preventive shutdown, engine operation is maintained by gas from the storage tank.
.“To be prepared for future NOx limits, ETW has already reserved the necessary space in the CHP container for the SCR catalyst. The plans also take into account the exhaust backpressure reserve,” explains Alexander Szabo, responsible sales manager at ETW Energietechnik.
“Changing the amount of substrate also contributes to the flexibility of the CHP plant. This makes it possible to reduce biogas production when electricity prices are low, so that the CHP plant can be shut down for up to two days when needed without overloading the gas storage tank. A heat storage tank can store 40,600 kilowatt hours of thermal energy, supplying the district heating network for around 50 hours without having to start up the CHP. The bottom line is that the CO2 savings of a renewable storage power plant can be estimated at 2,683 tons per year for electricity generation and around 1,300 tons for heat generation, including process heat,” he says.